Our Services
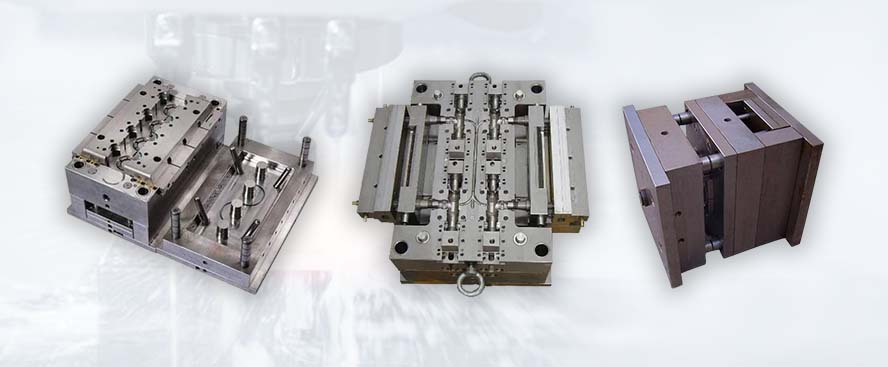
Plastic Injection Moulding Die
Plastic injection molding is a manufacturing process used to create a wide range of plastic parts and products. A crucial component of this process is the injection molding die, which is also commonly referred to as a mold or tool. The die is a precision-made, custom tool that is used to shape and form the plastic material into the desired product.
Here’s a basic overview of a plastic injection molding die:
- Die Design: The die is designed based on the specifications of the desired plastic part. This includes considerations for part geometry, size, complexity, and any special features such as threads, undercuts, or texture.
- Material Selection: The die is typically made from high-quality, durable materials such as steel or aluminum. The choice of material depends on factors like the expected production volume, the type of plastic being used, and the cost considerations.
- Tooling Process: The die is manufactured using various machining processes. This includes CNC machining, electrical discharge machining (EDM), and wire cutting to create the intricate features required for the part. The die is carefully shaped to match the desired part geometry.
- Mold Cavity: The die consists of one or more cavities that define the shape of the plastic part. The cavities are precisely designed to account for material shrinkage during cooling.
- Injection Molding Machine: The die is mounted onto an injection molding machine. The machine heats the plastic material to a molten state and then injects it into the die under high pressure.
- Cooling: After injection, the die is cooled to allow the plastic to solidify and take the shape of the cavity. Cooling can be done using water channels within the die.
- Ejection: Once the plastic is cooled and solidified, the die opens, and the formed part is ejected. Ejection pins or mechanisms within the die help in removing the part.
- Quality Control: The quality of the plastic part is closely monitored, and any defects are addressed. This may involve post-processing steps like trimming, machining, or assembly.
- Repeat Process: The die can be used to produce many parts, with the same process repeating for each cycle. Injection molding is known for its high production efficiency.
- Maintenance: Injection molding dies require regular maintenance to ensure they remain in good working condition. This may involve cleaning, repairing, or retooling the die as necessary.
Injection molding dies are custom-made for each specific part, and the cost of designing and manufacturing a die can vary widely depending on factors like complexity, size, and material. They are a significant investment but offer a cost-effective way to produce plastic parts in large quantities.
Specifications
- Part Geometry
- Material Selection
- Production Volume
- Tolerances
- Number of Cavities
- Die Material